Choosing the right high-pressure pump is crucial for industrial efficiency, whether in water treatment, food production, or oil and gas. Our buying guide helps you select the best pump by considering size, functionality, and durability. It’s designed to transform motor energy into hydraulic energy effectively, with a focus on compatibility with your work environment and fluid properties. Let our guide simplify your selection process, addressing everything from chemical duty motors to atmospheric constraints.
Key Takeaways
- Understanding your work environment is critical to the selection of a high-pressure pump.
- Fluid properties such as viscosity and flammability play a pivotal role in determining the type of pump required.
- Different motor types are suited to various operational environments, such as hazardous atmospheres and humid conditions.
- Consider pumps’ maintenance requirements, energy efficiency, and ease of use before making a selection.
- Ensure the high-pressure pump aligns with environmental regulations and can withstand your working conditions.
Evaluating Industrial High-Pressure Pump Needs
A successful industrial operation hinges on smart equipment choices. A central part of this wisdom lies in the selection of high-pressure pumps, the operational heartbeats of many industries. This process involves thoughtful comparison of pump features, understanding of environmental factors, and deep knowledge of fluid properties. We will break down these vital steps to guide you in selecting the best high-pressure pump for your industrial application.
Pump Environment Assessment for Optimal Performance
Pumps need to be evaluated based on the environment they will be placed in to ensure optimal performance. Will your pump be submerged in water or exposed to extreme temperatures? It may even operate in a hazardous environment or need to adhere to strict environmental regulations. Specialized pumps with specific motors like chemical, tropical, and wash-down duty motors are necessary for corrosive, humid, or hazardous atmospheres. Besides, temperature and altitude constraints impact pump motor selection and flow performance respectively. Furthermore, your pump’s power needs should correctly match your source of electricity to ensure consistent operation.
Understanding Fluid Properties and Pump Compatibility
Fluid properties and pump compatibility are other significant factors to consider in your pump selection process. Fluid viscosity, for instance, directly impacts flow resistance and necessitates the use of specific pumps. For example, centrifugal pumps are better suited for low-viscosity fluids, and positive-displacement pumps work better with higher-viscosity fluids. Similarly, fluid concentration and chemical composition determine the need for certain construction materials in pumps – like stainless steel for highly flammable fluids. In essence, understanding your fluid’s properties can lay the groundwork for ensuring your pump’s longevity and reliability across various industrial applications.
Crucial Pump System Properties: Flow, Head, and Efficiency
There are three key pump system properties to consider: flow, head, and efficiency. The volume of liquid pumped and the required system operation should match your pump’s flow rate and pressure. Different types of heads—suction head, system head, and discharge head—require careful calculation to prevent efficiency losses. Furthermore, factors like energy efficiency, ease of use, and maintenance considerations must be evaluated harmoniously with these properties when settling on your pump selection.
Calculating Net Positive Suction Head (NPSH) for Your Environment
Cavitation is a common problem with high-pressure pumps, but it’s something you can avoid with careful calculation of the Net Positive Suction Head (NPSH). Ultimately, your available NPSH (NPSHa) must exceed your required NPSH (NPSHr). Altitude and environmental considerations play a role in these calculations. As the altitude increases and the air pressure decreases, it might affect your pump’s suction capabilities and the cooling effectiveness of the pump motor. So, before selecting a high-pressure pump for your industrial application, these factors need careful evaluation. To conclude, understanding the dynamics behind pump environmental considerations, fluid properties, pump system properties, and calculations of NPSH are fundamental to determining the perfect high-pressure pump for your industry. By taking all these aspects into account, you’ll be more equipped to make an informed decision that can enhance productivity, maintain safety, and, ultimately, boost your bottom line.
Choosing the right high-pressure pump
Finding the perfect high-pressure pump for your needs isn’t a decision to be taken lightly. From assessing your specific requirements to evaluating various affordable high-pressure pump models on the market, the process can be overwhelming. There are several factors you ought to consider when embarking on this selection journey.
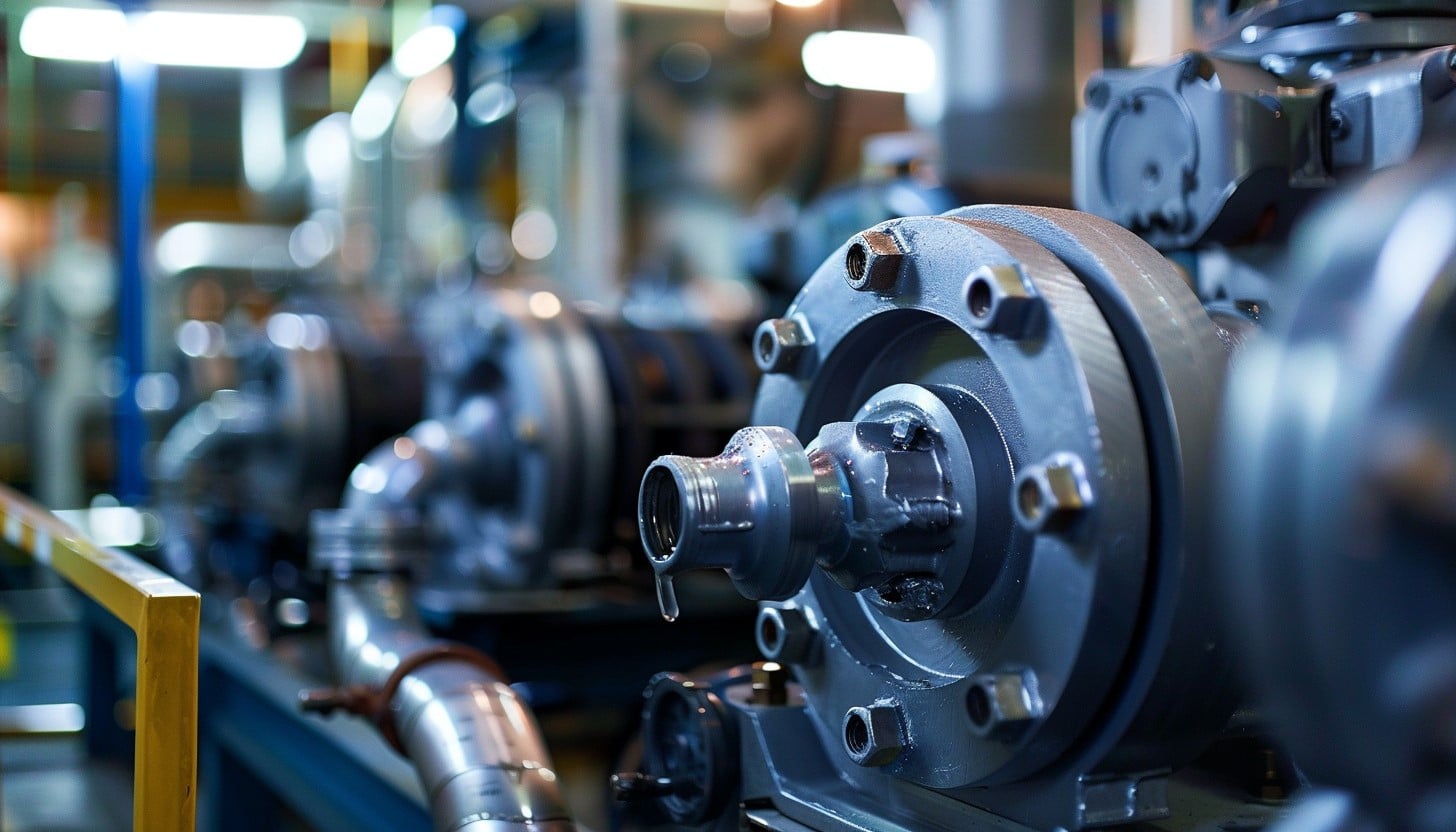
The selection of the correct high-pressure pump involves a comprehensive understanding of the media to be transferred, including its chemical composition, viscosity, and the presence of solids. The choice between different types of pumps, such as submersible pumps for high-solid media and surface-mounted pumps for water supply and pressure boosting, is critical. Each pump type is designed to meet specific requirements across various industries. Consideration of the pump’s application, cost, warranty, and service support is essential. Knowledge of the media characteristics, flow requirements, pressure specifications, and the operational environment is key to making an informed decision. Ultimately, selecting the right high-pressure pump requires careful evaluation of one’s needs and a thorough understanding of the available options, ensuring the selection of the most suitable pump for the intended application.
Exploring High-Pressure Pump Options and their Use-Cases
Industrial applications often involve the movement of fluids, the control of temperatures, and the handling of viscous substances. For these myriad needs, high-pressure pumps in their various forms—centrifugal, heat, cooling tower, diaphragm and gear, peristaltic, and piston—provide efficient and reliable solutions.
Centrifugal Pumps for Versatility in Fluid Movement
We turn first to centrifugal high-pressure pumps when large volumes of low-viscosity fluids must be pumped at consistent flow rates. Making them a versatile pump option for numerous applications, including water treatment processes and petrochemical operations. The compact size, quiet operation, and low maintenance requirements of centrifugal pumps reinforce their suitability for diverse industrial settings.
Heat and Cooling Tower Pumps: Tailored for Temperature Control
Temperature control is essential in systems like air-conditioning units, and for these requirements, we introduce heat and cooling tower pumps. Such pumps are integral to moving heat away when repurposing it is not an option. System requirements shape heat pump selection and dictate the size and capability of cooling tower pumps, ensuring desired temperatures are consistently maintained.

Diaphragm and Gear Pumps for Handling Dense and Viscous Fluids
The transportation of dense and viscous fluids such as paints, greases, and certain chemicals demands specialized solutions—diaphragm and gear pumps. With diaphragm pumps offering dry running capabilities and gear pumps supplying a compact yet reliable solution, they come into their own when handling viscous industrial fluids. Their precision is especially valued in the chemical, mining, food, and plastics processing industries.
Selecting Peristaltic and Piston Pumps for Precision Applications
Last but not least, when medium-flow and high-pressure operations call for precision, peristaltic and piston pumps come into play. Peristaltic pumps maintain a sterile environment, thereby making them a popular choice in the medical and chemical industries. Conversely, piston pumps excel in medium-flow operations, leading to their widespread use in the oil industry.
Pump Type | Advantages | Typical Applications |
---|---|---|
Centrifugal Pumps | Efficient for large volumes, low noise | Water treatment, Petrochemical process |
Heat and Cooling Tower Pumps | Precise temperature control | Air-conditioning units |
Diaphragm and Gear Pumps | Competent in handling viscous fluids | Chemical and food processing units |
Peristaltic and Piston Pumps | Precision in medium-flow and high-pressure operations | Medical, Chemical, and oil industry |
Conclusion
In the selection and application of high-pressure pumps, it’s vital to not just pick a model that meets your needs but also to economize your investment with its long-term maintenance and reliability. The right choice leads to higher efficiency in industrial pumps and fewer operational hardships. Let us look deeper into these critical factors.
Maintenance, Efficiency, and Long-Term Reliability
High-pressure pump maintenance plays a vital role in preserving its efficiency and reliability. A well-maintained pump runs smoother, saves energy, and prevents unexpected downtimes, contributing significantly to overall industrial efficiency. The longevity of your pump hinges considerably on its regular upkeep and the choice of energy-efficient models. The selection process must consider the level of expertise required for maintenance in future and if specialist support will be necessary post-installation.
Final Considerations and the Importance of Expert Support
When you’re finalizing your high-pressure pump selection, all factors, such as environmental conditions, fluid properties, system requirements, and long-term operational costs, should be considered. Particularly, high-pressure pump performance can be enhanced greatly when there is expertise available for pump repair and maintenance. Experts like those from Houston Pump & Gear, renowned for their exceptional service in this industry, help significantly to address pump repair inquiries and manage efficient service options.
Investing Wisely in Quality High-Pressure Pumps
The decision to invest in a high-pressure pump requires a comprehensive analysis of not just its specifications and performance ratings but also reviews of the brand’s reputation. Top high-pressure pump brands guarantee quality and dependable performance and reduce the likelihood of operational failures. They not only promise long-term operational benefits but also bring considerable cost savings from energy efficiency and manufacturer support. A wise investment in industrial pumps is indeed a valuable resource for your industry.